clutch digram
Moderators: Site Director, FZR Forum Moderators
-
- Site Newbie
- Posts: 44
- Joined: Thu Dec 18, 2008 7:34 pm
clutch digram
i was searching i could not find any pics or help about clutch. can i take cover off without draining oil? any schematic or replacement instructions. my clutch system is screwed up but no idea what parts are missing or need adjusted. i know a manual would help but answers from real people not pro mechanics (no insult intended) tend to help more.
Re: clutch digram
Chapter 3 and 4 at this:
http://www.fzrarchives.com/ipb/index.ph ... opic=36296
Yes, if on sidestand you can remove the clutch cover (right side-big one) w/o draining oil. Be careful with the gasket. Slight damage to the gasket and you can use 3bond (yamabond-the thin grey 'anerobic' sealer).
The clutch actuator is on the opposite side under the front sprocket cover (no oil-just a mess of road grime and chain lube behind it).
You said the clutch pulls in but stays? Check for springs intact under right cover....count the plates 9 friction, 8 steels. And that alll the parts on the list are there.
You can find microfiche here:
http://www.yamaha-motor.com/sport/parts/home.aspx
http://www.fzrarchives.com/ipb/index.ph ... opic=36296
Yes, if on sidestand you can remove the clutch cover (right side-big one) w/o draining oil. Be careful with the gasket. Slight damage to the gasket and you can use 3bond (yamabond-the thin grey 'anerobic' sealer).
The clutch actuator is on the opposite side under the front sprocket cover (no oil-just a mess of road grime and chain lube behind it).
You said the clutch pulls in but stays? Check for springs intact under right cover....count the plates 9 friction, 8 steels. And that alll the parts on the list are there.
You can find microfiche here:
http://www.yamaha-motor.com/sport/parts/home.aspx
http://www.michiganmobileservice.com/

“A common mistake that people make when trying to design something completely foolproof is to underestimate the ingenuity of complete fools.”-Douglas Adams
http://www.youtube.com/user/reelrazor
“A common mistake that people make when trying to design something completely foolproof is to underestimate the ingenuity of complete fools.”-Douglas Adams
http://www.youtube.com/user/reelrazor
Re: clutch digram
Clutch slipping - The manual says:
1. Incorrect clutch adjustment
2. Weak clutch springs
3. Worn clutch plates
4. Damaged pressure plate
5. Clutch release mechanism damage
If you just need to adjust the cable more, that's easy. First, loosen the adjuster and the hand lever. Then, remove the lower left fairing. On the front of the sprocket cover there's a round black rubber cap. Remove it. Under it you'll have a, I wanna say 12mm, nut; loosen it. Turn the phillips screw until the slightest bit of resistance if felt. Turn it out again and tighten once more until the slightest bit of resistance is felt, then back out a 1/4 of a turn. Tighten the nut without moving the screw, check for free play at the hand lever, adjust as needed. You may wann give it a try while the fairings off. The first time I did this I tightened to much and had to pull it all off again.
Changing Clutch Plates
The clutch is a wet-multi-plate type which operates immersed in engine oil. It is mounted on the right-hand side of the transmission main shaft. The clutch can be serviced with the engine in the frame.
The clutch release mechanism is mounted in the drive sprocket cover and is cable operated by the left-hand clutch lever. The release pushrod rides within the transmission main shaft.
Removal
1. Remove the lower fairings on both sides.
2. Drain the oil.
3. Remove the drive sprocket cover.
4. Using a criss cross pattern, loosen then remove the bolts securing the clutch cover. Remove the cover and gasket, don't loose the locating dowels.
5. Loosen the 6 pressure plate screws in a criss cross pattern. Then remove the screws and springs.
6. Remove the pressure plate.
7. Remove all of the clutch plates, has notches on the outside, and friction discs, has notches on the inside. Stack the plates and discs in order of removal.
8. Remove the short pushrod from the end of the transmission shaft.
9. Using a magnet, pull the steel ball out of the end of the trasmission main shaft.
10. Straighten out the locking tab on the locknut.
Note: To keep the clutch housing from turning when removing the clutch hub nut in Step 11, use a "Grabbit" tool, or equivalent.
11. Loosen, then remove the clutch nut.
12. Slide off the lock washer.
13. Remove the clutch boss.
14. Slide off the grooved thrust washer.
15. Use a dental tool or pick and withdraw the spacer and then the bearing from the center of the clutch housing.
16. Move the clutch housing over to one side to clear the crankcase and remove the clutch housing.
17. Slide the thrust washer and collar off the transmission shaft.
18. Pull the long pushrod out of the transmission main shaft tunnel.
Inspection
1. Clean all clutch parts in petroleum-based solvent such as commercial solvent or kerosene and thoroughly dry with compressed air.
2. Measure the free length of each clutch spring. 5 springs, standard length is 35 mm or 1.32 in.; Minimum length is 32.6 mm or 1.28 in. Replace any springs that have sagged to the service limit or less.
3. Measure the thickness of each friction disc at several places around the disc. 9 discs, standard thickness is 2.9-3.1 mm or 0.1142-0.1220 in; minimum 2.8 mm or 0.11 in. Replace any discs that have worn to the service limit or less.
4. Measure the thickness of each clutch plate at several places around the plate. 8 plates, standard thickness is 1.8-2.2 mm or 0.072-0.085 in. Replace any plates that are worn. Yamaha does not provide wear limit specifications for the clutch plates.
5. Check the clutch plates for warpage on a surface plate such as a piece of plate glass. Warp limit minimum is 2.8 mm or 0.11 in. Replace any plate that is warped to the service limit or more.
6. Inspect the clutch housing for the folowing:
a. Check the fingers for cracks, nicks or galling where they come in contact with the friction dics tabs. They must be smooth for chatter free operation. If any severe damage is evident, the components should be replaced.
b. Check the outer gear and the oil pump drive gear for tooth wear, damage or cracks. Replace the clutch housing if necessary.
c. Inspect the damping springs for breakage or wear. Replace the clutch housing if necessary.
d. Check the center bearing bore for cracks, deep scoring, excessive wear or heat discoloration. If the bearing bore is damaged, also check the clutch bearing and bearing spacer for damage. Replace worn or damaged parts.
7. Inspect the clutch boss for the following:
a. Check the grooves for cracks, nicks or galling where they come in contact with the friction dics tabs. They must be smooth for chatter free operation. If any severe damage is evident, the components must be replaced.
b. Inspect the posts for wear or galling. If any severe damage is evident, the components must be replaced.
c. Inspect the inner splines for damage. Remove any small nicks with an oilstone. If damage is severe, the clutch boss must be replaced.
8. Inspect the posts and grooves in the pressure plate. If they show signs of cracks, wear or galling the pressure plate should be replaced.
9. Inspect the long pushrod for bending or damage. If the pushrod is bent to the limit of 1.28 mm or 0.020 in., it will hang up in the transmission shaft tunnel. Replace rod if necessary.
10. Inspect the short push rod where it contacts the long pushrod and push lever assembly. Inspect the O-ring seal for wear and hardness or discoloration. Replace the O-ring if it's condition is doubtful.
11. Check the grooved thrust washer for galling or damage, replace if necessary.
12. Inspect the spacer, thrust washer and collar for wear or damage and replace if necessary.
Installation
1. Install the long pushrod into the transmission main shaft tunnel.
2. Slide the collar and the thrust washer onto the transmission shaft.
3. Install the clutch housing onto the transmission shaft.
4. Install the bearing into the clutch housing.
5. Center the clutch housing over the transmission shaft and install the spacer into thebearing.
6. Slide the grooved thrust washer onto the transmission shaft.
7. Install the clutch boss.
8. Install the lock washer and index the locking tab into the receptacle in the clutch boss.
9. Install the clutch nut.
10. Use the same tool setup used during removal to hold the clutch boss in place and tighten the clutch nut to 70 N•M or 50 ft.-lbs. Remove special tool.
11. Bend down one of the locking tabs against one of the flats on the locknut.
12. Install the steel ball into the end of the transmission main shaft.
13. Make sure the O-ring seal is in place and install the short pushrod into the end of the
transmission shaft.
Note: If new friction discs and clutch plates are being installed, apply new engine oil to all surfaces to avoid having the clutch lock up when used for the first time.
14. Onto the clutch hub, install the first friction disc, then a clutch plate.
15. Continue to install the discs and plates in that order. The last item is a friction disc.
16. Install the pressure plate.
17. Install the springs and screws into the pressure plate.
18. Tighten the 6 pressure plate screws in several stages and in a criss cross pattern. Tighten the screws to 6 N•M or 4.3 ft.-lbs.
19. Make sure the dowel pins are in place and install a new gasket.
20. Install the clutch cover and bolts. Tighten the bolts securely in a criss cross pattern.
21. Install the engine sprocket cover.
22. Refill the engine oil.
23. Adjust the clutch.
24. Install the fairings.
1. Incorrect clutch adjustment
2. Weak clutch springs
3. Worn clutch plates
4. Damaged pressure plate
5. Clutch release mechanism damage
If you just need to adjust the cable more, that's easy. First, loosen the adjuster and the hand lever. Then, remove the lower left fairing. On the front of the sprocket cover there's a round black rubber cap. Remove it. Under it you'll have a, I wanna say 12mm, nut; loosen it. Turn the phillips screw until the slightest bit of resistance if felt. Turn it out again and tighten once more until the slightest bit of resistance is felt, then back out a 1/4 of a turn. Tighten the nut without moving the screw, check for free play at the hand lever, adjust as needed. You may wann give it a try while the fairings off. The first time I did this I tightened to much and had to pull it all off again.
Changing Clutch Plates
The clutch is a wet-multi-plate type which operates immersed in engine oil. It is mounted on the right-hand side of the transmission main shaft. The clutch can be serviced with the engine in the frame.
The clutch release mechanism is mounted in the drive sprocket cover and is cable operated by the left-hand clutch lever. The release pushrod rides within the transmission main shaft.
Removal
1. Remove the lower fairings on both sides.
2. Drain the oil.
3. Remove the drive sprocket cover.
4. Using a criss cross pattern, loosen then remove the bolts securing the clutch cover. Remove the cover and gasket, don't loose the locating dowels.
5. Loosen the 6 pressure plate screws in a criss cross pattern. Then remove the screws and springs.
6. Remove the pressure plate.
7. Remove all of the clutch plates, has notches on the outside, and friction discs, has notches on the inside. Stack the plates and discs in order of removal.
8. Remove the short pushrod from the end of the transmission shaft.
9. Using a magnet, pull the steel ball out of the end of the trasmission main shaft.
10. Straighten out the locking tab on the locknut.
Note: To keep the clutch housing from turning when removing the clutch hub nut in Step 11, use a "Grabbit" tool, or equivalent.
11. Loosen, then remove the clutch nut.
12. Slide off the lock washer.
13. Remove the clutch boss.
14. Slide off the grooved thrust washer.
15. Use a dental tool or pick and withdraw the spacer and then the bearing from the center of the clutch housing.
16. Move the clutch housing over to one side to clear the crankcase and remove the clutch housing.
17. Slide the thrust washer and collar off the transmission shaft.
18. Pull the long pushrod out of the transmission main shaft tunnel.
Inspection
1. Clean all clutch parts in petroleum-based solvent such as commercial solvent or kerosene and thoroughly dry with compressed air.
2. Measure the free length of each clutch spring. 5 springs, standard length is 35 mm or 1.32 in.; Minimum length is 32.6 mm or 1.28 in. Replace any springs that have sagged to the service limit or less.
3. Measure the thickness of each friction disc at several places around the disc. 9 discs, standard thickness is 2.9-3.1 mm or 0.1142-0.1220 in; minimum 2.8 mm or 0.11 in. Replace any discs that have worn to the service limit or less.
4. Measure the thickness of each clutch plate at several places around the plate. 8 plates, standard thickness is 1.8-2.2 mm or 0.072-0.085 in. Replace any plates that are worn. Yamaha does not provide wear limit specifications for the clutch plates.
5. Check the clutch plates for warpage on a surface plate such as a piece of plate glass. Warp limit minimum is 2.8 mm or 0.11 in. Replace any plate that is warped to the service limit or more.
6. Inspect the clutch housing for the folowing:
a. Check the fingers for cracks, nicks or galling where they come in contact with the friction dics tabs. They must be smooth for chatter free operation. If any severe damage is evident, the components should be replaced.
b. Check the outer gear and the oil pump drive gear for tooth wear, damage or cracks. Replace the clutch housing if necessary.
c. Inspect the damping springs for breakage or wear. Replace the clutch housing if necessary.
d. Check the center bearing bore for cracks, deep scoring, excessive wear or heat discoloration. If the bearing bore is damaged, also check the clutch bearing and bearing spacer for damage. Replace worn or damaged parts.
7. Inspect the clutch boss for the following:
a. Check the grooves for cracks, nicks or galling where they come in contact with the friction dics tabs. They must be smooth for chatter free operation. If any severe damage is evident, the components must be replaced.
b. Inspect the posts for wear or galling. If any severe damage is evident, the components must be replaced.
c. Inspect the inner splines for damage. Remove any small nicks with an oilstone. If damage is severe, the clutch boss must be replaced.
8. Inspect the posts and grooves in the pressure plate. If they show signs of cracks, wear or galling the pressure plate should be replaced.
9. Inspect the long pushrod for bending or damage. If the pushrod is bent to the limit of 1.28 mm or 0.020 in., it will hang up in the transmission shaft tunnel. Replace rod if necessary.
10. Inspect the short push rod where it contacts the long pushrod and push lever assembly. Inspect the O-ring seal for wear and hardness or discoloration. Replace the O-ring if it's condition is doubtful.
11. Check the grooved thrust washer for galling or damage, replace if necessary.
12. Inspect the spacer, thrust washer and collar for wear or damage and replace if necessary.
Installation
1. Install the long pushrod into the transmission main shaft tunnel.
2. Slide the collar and the thrust washer onto the transmission shaft.
3. Install the clutch housing onto the transmission shaft.
4. Install the bearing into the clutch housing.
5. Center the clutch housing over the transmission shaft and install the spacer into thebearing.
6. Slide the grooved thrust washer onto the transmission shaft.
7. Install the clutch boss.
8. Install the lock washer and index the locking tab into the receptacle in the clutch boss.
9. Install the clutch nut.
10. Use the same tool setup used during removal to hold the clutch boss in place and tighten the clutch nut to 70 N•M or 50 ft.-lbs. Remove special tool.
11. Bend down one of the locking tabs against one of the flats on the locknut.
12. Install the steel ball into the end of the transmission main shaft.
13. Make sure the O-ring seal is in place and install the short pushrod into the end of the
transmission shaft.
Note: If new friction discs and clutch plates are being installed, apply new engine oil to all surfaces to avoid having the clutch lock up when used for the first time.
14. Onto the clutch hub, install the first friction disc, then a clutch plate.
15. Continue to install the discs and plates in that order. The last item is a friction disc.
16. Install the pressure plate.
17. Install the springs and screws into the pressure plate.
18. Tighten the 6 pressure plate screws in several stages and in a criss cross pattern. Tighten the screws to 6 N•M or 4.3 ft.-lbs.
19. Make sure the dowel pins are in place and install a new gasket.
20. Install the clutch cover and bolts. Tighten the bolts securely in a criss cross pattern.
21. Install the engine sprocket cover.
22. Refill the engine oil.
23. Adjust the clutch.
24. Install the fairings.
-
- Site Newbie
- Posts: 44
- Joined: Thu Dec 18, 2008 7:34 pm
Re: clutch digram
thanks a ton ask and ye shall receive. i appreciate it . ill post later and tell you what i found.
Re: clutch digram
Nice write up Mark!! I'm making this a sticky for now. This should be part of the WIKI as well
Duane...
Bike:
1994 Yamaha FZR 1000 EXUP
Factory Pro Stage 1 Jetting | K&N Filter | Corbin Seat | ProTek Keyless Gas Cap | GSXR Mirrors
My Thread
Cage:
2005 Saab 9-7x 5.3i Arc AWD
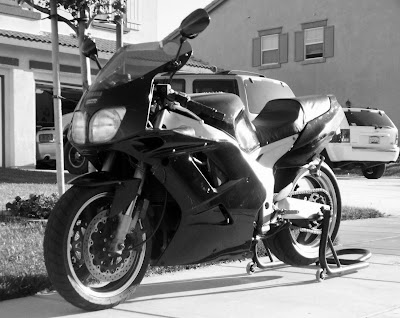
THE WIKI IS YOUR FRIEND
THE SEARCH IS YOUR SIGNIFICANT OTHER
USE THEM!!
Bike:
1994 Yamaha FZR 1000 EXUP
Factory Pro Stage 1 Jetting | K&N Filter | Corbin Seat | ProTek Keyless Gas Cap | GSXR Mirrors
My Thread
Cage:
2005 Saab 9-7x 5.3i Arc AWD
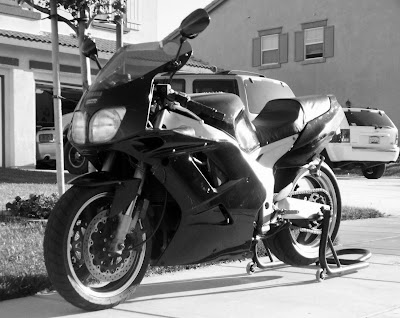
THE WIKI IS YOUR FRIEND
THE SEARCH IS YOUR SIGNIFICANT OTHER
USE THEM!!